Pioneers in CO2nversion
Green Hydrocarbons for the Chemical and Transport Sector
​
Concrete Chemicals is a CCU project (carbon capture and utilization) and deals with the production of e-fuels at the Ruedersdorf site. In a first step, a synthesis gas is produced from captured CO2 and green hydrogen, hydrogen being obtained from the electrolysis of converted wind power. This synthesis gas is transformed into synthetic green hydrocarbons by means of the Fischer-Tropsch-procedure.
In a broader perspective, the deployment of Concrete Chemicals will enable further development of highly innovative catalytic processes, reactor technology and catalytic materials with superior efficiency. The project offers the unique opportunity to serve as a flagship and blueprint for the cement industry in Europe and worldwide - demonstrating the technological possibilities to turn CO2 into utilizable products. Achieving a low-carbon cement production in the long term, Concrete Chemicals contributes to reaching Brandenburg’s CO2 reduction ambitions and the European Green Deal’s targets alike.
The project partners have submitted funding applications under the German government's funding schemes.
​
The Carbon Neutral Alliance at
the Cement Plant Rüdersdorf
​
CEMEX is a leading vertically integrated heavy building materials company focused on four core businesses: Cement, Ready-Mix Concrete, Aggregates, and Urbanization Solutions. In Europe, CEMEX operates a total of ten cement plants with integrated clinker production.
As part of its “Future in Action" program, CEMEX is developing a masterplan called Carbon Neutral Alliance at the cement plant in Rüdersdorf near Berlin to test and accelerate innovative technologies to reach carbon neutrality. The technological learnings derived from the Rüdersdorf Carbon Neutral Alliance should gradually be shared with the CEMEX global portfolio of cement plants and adapted to local conditions to accelerate its decarbonization goals of the cement production process.
​​
The cement industry, and thus the entire downstream value chain of cement and concrete, are facing major challenges on the path to climate neutrality due to the large amounts of CO2 that are released during the production of clinkers. Around two thirds are accounted for by raw material-related process emissions resulting from the chemical process. Further emissions are caused by the use of fossil fuels. Nevertheless, the demand for cement and concrete is growing as the world’s population increases and becomes more urban, with emerging economies developing more and more infrastructures. This highlights the urgency and chances of decarbonizing cement production to reach the EU’s emission reduction targets by 2050.
Tradition Meets Innovation
in Rüdersdorf
​
Limestone has been quarried and processed into building materials in Rüdersdorf for over 750 years.
The first lime kilns were built here as early as the 16th century, and cement production began in 1885.
​
Today, the cement plant at the Rüdersdorf location represents the state of the art in cement process technology. In all production stages - from open-cast mining to raw grinding, the burning process, and cement grinding, all the way to dispatch - equipment is used that simultaneously combines competitive cement production, high energy efficiency, and an environmentally compatible production process. A continuous improvement process ensures that this remains.

Technical Concept of Concrete Chemicals
The uniqueness of Concrete Chemical’s technical concept is that it combines a carbon capture process with the production of green hydrocarbons and methanol which results in CO2 reduction combined with efficiency as its best.
To produce the sustainable aviation fuel, Zaffra will contribute its innovative Fischer-Tropsch technology in combination with Sasol’s technology partner, Haldor Topsoe’s syngas generation and hydroprocessing technologies. The e-kerosene will be certified for use in aircraft and in accordance with current approvals, can be blended to constitute up to 50% of the jet fuel. Furthermore, the project partners intend that the e-kerosene will meet the EU RED II criteria and thus allow it to be accounted for in the greenhouse gas reduction quota and the mandatory minimum blending quota for PtL kerosene.

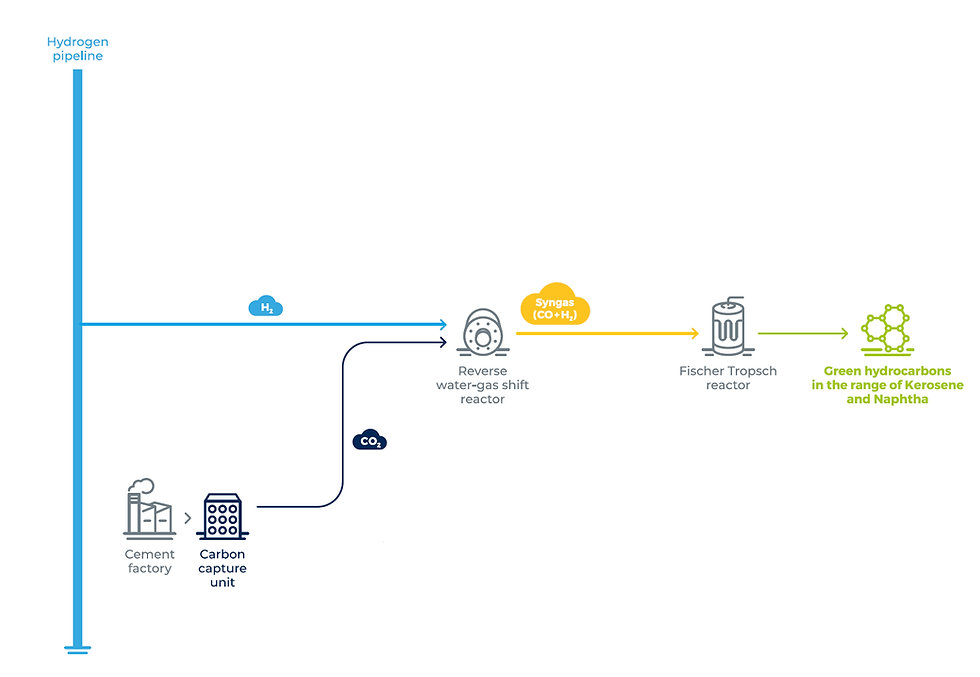
